鋁單板氟碳粉末噴涂工藝是一種常見的表面處理方法,能夠為鋁單板提供優異的耐候性、裝飾性和防護性能。以下是該工藝的詳細步驟:
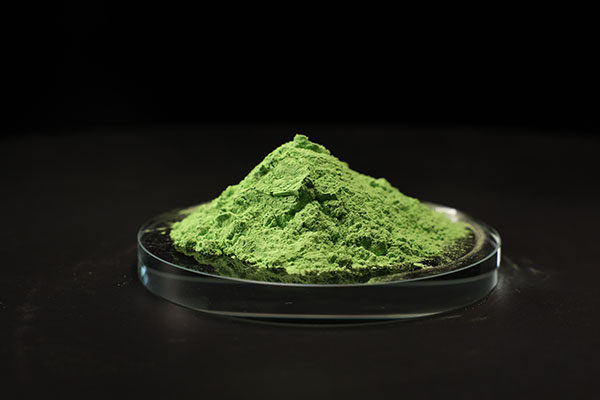
1.表面預處理
清洗:
使用有機溶劑(如丙酮、丁酮等)或的金屬清洗劑,鋁單板表面的油污、油脂和污垢。這一步驟很關鍵,因為油污會影響后續涂層的附著力。
接著采用噴淋或浸泡的方式,用清水沖洗鋁單板,確保表面的清洗劑。
堿蝕:
將鋁單板浸泡在堿性蝕刻溶液中,一般是氫氧化鈉(NaOH)溶液,濃度通常在3%-5%左右,溫度控制在40-60℃。堿蝕時間根據鋁板的材質和表面狀態而定,一般為1-3分鐘。
堿蝕的目的是鋁板表面的自然氧化膜,使鋁板表面形成微觀的粗糙結構,增加涂層的附著力。堿蝕后,要用大量清水沖洗鋁板,以表面殘留的堿液。
中和:
使用酸性溶液(如硝酸溶液,濃度約為15%-20%)對堿蝕后的鋁板進行中和處理,時間約為30-60秒。中和處理可以鋁板表面殘留的堿性物質,調整鋁板表面的酸堿度。
中和后同樣需要用清水沖洗鋁板,確保表面呈中性,避免殘留的酸液對后續涂層產生不良影響。
鉻化處理(可選):
在一些對附著力和耐腐蝕性要求較高的情況下,會對鋁板進行鉻化處理。將鋁板浸泡在鉻酸鹽溶液中,形成一層的鉻化膜。鉻化膜可以進一步提高鋁板表面的耐腐蝕性和涂層附著力。
不過,由于鉻化物對環境和人體有危害,現在也有一些無鉻化的替代處理方法,如采用鋯鹽、鈦鹽等進行處理。
2.粉末噴涂準備
預熱:
將預處理后的鋁單板放入烘干爐中進行預熱,溫度一般控制在100-120℃,時間為10-15分鐘。預熱可以使鋁板表面干燥,有利于粉末涂料的吸附和熔融。
靜電噴涂設備調試:
檢查并調整靜電噴槍的參數,包括電壓、電流、出粉量、霧化效果等。一般靜電電壓設置在60-90kV,確保粉末涂料能夠充分帶電,提高粉末的吸附效率。
根據鋁單板的尺寸和形狀,調整噴槍與鋁板之間的距離和噴涂角度。噴槍與鋁板的距離通常保持在15-25cm,角度盡量垂直于鋁板表面,以保證粉末均勻地噴涂在鋁板上。
3.粉末噴涂
噴涂操作:
將氟碳粉末涂料通過靜電噴槍均勻地噴涂在預熱后的鋁單板表面。在噴涂過程中,要保持噴槍的移動速度均勻,避免局部噴涂過厚或過薄。
一般采用多次噴涂的方式,每次噴涂的厚度控制在30-60μm左右,總厚度根據產品要求達到60-120μm。例如,對于裝飾性要求較高的建筑幕墻鋁單板,可能需要較厚的涂層,總厚度可達到100-120μm。
對于有復雜形狀或邊角的鋁單板,要注意對這些部位進行充分噴涂,確保涂層覆蓋完整。可以通過調整噴槍角度或使用輔助噴槍來實現。
4.固化處理
固化爐設置:
將噴涂好粉末的鋁單板放入固化爐中,固化爐的溫度根據氟碳粉末涂料的類型和要求進行設置,一般在180-220℃之間。
固化時間也很關鍵,通常為10-20分鐘。固化過程中,粉末涂料在高溫下熔融、流平并發生交聯反應,形成堅硬、致密的涂層。
固化過程監控:
在固化過程中,要使用溫度傳感器等設備監控固化爐內的溫度變化,確保溫度均勻且符合設定的固化曲線。如果溫度過高或過低,都可能導致涂層質量不佳,如出現表面不平整、硬度不足、附著力下降等問題。
5.質量檢查與后處理
外觀檢查:
檢查鋁單板涂層的外觀,包括顏色、光澤度、平整度等。顏色應符合設計要求,光澤度均勻一致,表面平整光滑,無橘皮、流掛、針孔等缺陷。
對于有金屬質感要求的氟碳粉末涂層,還要檢查金屬效果是否自然、均勻,在不同角度下的視覺效果是否良好。
性能測試:
進行附著力測試,常用的方法是劃格試驗。用刀具在涂層上劃格,然后用膠帶粘貼并撕下,觀察涂層脫落情況,一般要求附著力等級達到0-1級。
測試涂層的耐候性、耐化學腐蝕性等性能。耐候性可以通過人工加速老化試驗(如QUV試驗)來評估,經過時間的試驗后,涂層的光澤保持率和顏色變化應符合標準要求。耐化學腐蝕性則通過將鋁單板浸泡在特定的化學溶液(如酸、堿、鹽溶液)中時間后,觀察涂層的外觀和性能變化。
修補與包裝:
對于檢查出有輕微缺陷的鋁單板,可以進行局部修補。如對于小面積的涂層脫落或劃傷,可以采用補漆或重新噴涂的方法進行。
質量合格的鋁單板進行包裝,一般采用塑料薄膜、泡沫等材料進行保護,避免在運輸和儲存過程中對涂層造成損壞。